Similar to the progressive die stamping process, the transfer press stamping process gradually transforms raw material into the desired part or product by moving it from station to station. The main differences between the two manufacturing methods is that transfer press stamping operations separate the part from the main strip in the first step and transfer it from station to station using a mechanical transport system, while progressive die stamping operations automatically progress the main strip from station to station and then separate the part from it in the final step. Both offer unique advantages and disadvantages that make them suitable for different projects. Read on to learn more about what benefits the transfer press stamping process offers and which applications for which it is suited.
KEY BENEFITS OF TRANSFER PRESS STAMPING
Compared to other stamping methods, transfer press stamping offers a number of benefits, such as:
- Broader setup flexibility. Transfer press stamping operations can employ a single die, a series of dies, or a series of machines arranged in a row to accommodate different project requirements. Additionally, as the part is separated from the strip in the beginning, it can be transferred freely between stations.
- Simpler stamping operations. The transfer press stamping process has become much more efficient over the years. Before the development of automation technology, it used manual transfer mechanisms and multiple presses. Today, automatic transfer systems make it possible to condense a whole stamping operation into a single press.
- Better suitability for mass production. Transfer press stamping requires precise and accurate alignment and smooth mechanical transfer between steps. The use of automation technology efficiently fulfills these requirements, making it easy to accommodate high-volume orders without sacrificing part or process quality.
WHEN SHOULD I USE TRANSFER PRESS STAMPING VS. PROGRESSIVE DIE STAMPING?
Both transfer press stamping and progressive die stamping find application in the same industries. However, which one is used for a particular project depends on the part and production specifications. Some of the key factors to consider when choosing between the two manufacturing methods are:
- Part size. Transfer press stamping is generally utilized to produce large parts, such as frames, shells, tubes, and other structural components. In contrast, progressive die stamping is typically employed for the production of small parts.
- Part complexity. The transfer press stamping process can incorporate various operations into the stamping process to produce parts with cutouts, knurls, ribs, threads, and/or other complex or intricate design elements. This flexibility results in a smaller need for additional processing operations and, consequently, lower production costs.
- Production quantity. Both processes are suitable for high-volume production orders. Transfer press stamping is ideal for the mass production of large parts, while progressive die stamping is appropriate for manufacturing small parts in high volumes. However, high-volume progressive die stamping operations necessitate investment in permanent tool steel dies, which are more durable and, consequently, more expensive.
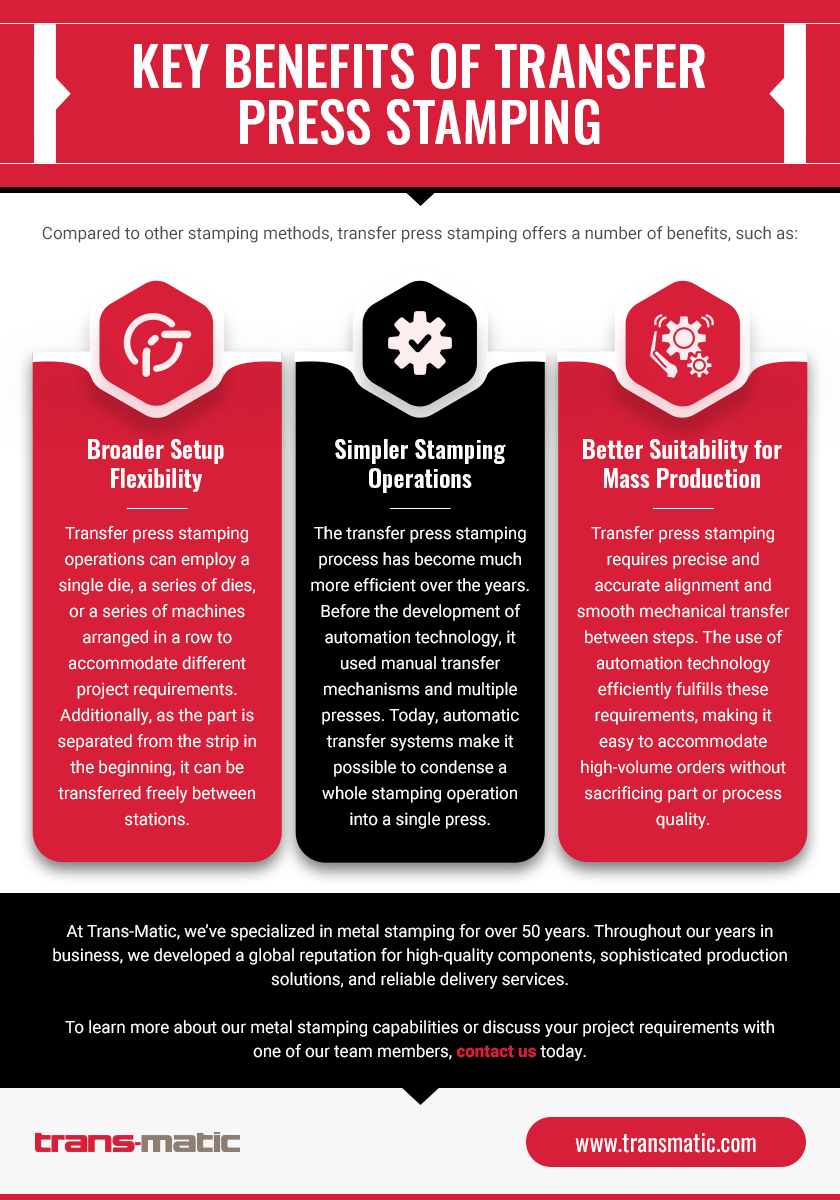
TRANSFER PRESS STAMPING SERVICES AT TRANS-MATIC
Transfer press stamping is an effective and efficient process for creating large components with intricate or complex designs. If you’re looking for an experienced and knowledgeable transfer press stamping partner for your next project, turn to the experts at Trans-Matic.
At Trans-Matic, we’ve specialized in metal stamping for over 50 years. Throughout our years in business, we developed a global reputation for high-quality components, sophisticated production solutions, and reliable delivery services. Our customers know they can depend on us to provide the metal stamped parts and products they need when they need them.
To learn more about our metal stamping capabilities or discuss your project requirements with one of our team members, contact us today. If you’re requesting a quote, it is important to note that we typically require a minimum EAV of 150,000 pieces.